Introducing an innovative method that combines durability, lightness, and the ability to integrate circuits into adaptable surfaces such as clothing and accessories.
The discovery, published in the prestigious journal Nature Electronics, promises to revolutionize the electronics market, paving the way for a new generation of devices that can be bent, stretched, and twisted without losing functionality. This breakthrough is set to transform fields such as soft robotics, medical devices, fashion, and entertainment, expanding the boundaries of what is possible in electronics.
The innovation in question is a multilayer “soft” circuit designed to allow extreme flexibility while maintaining durability. It features two main layers: the upper layer houses nine LEDs, while the lower layer contains nine sensors, all interconnected by 21 strategically placed liquid metal pathways that enable electrical flow between the layers. A notable feature is the circuit’s reduced thickness, comparable to a few sheets of paper, ensuring a lightweight and thin structure—ideal for wearable applications that demand comfort and mobility.
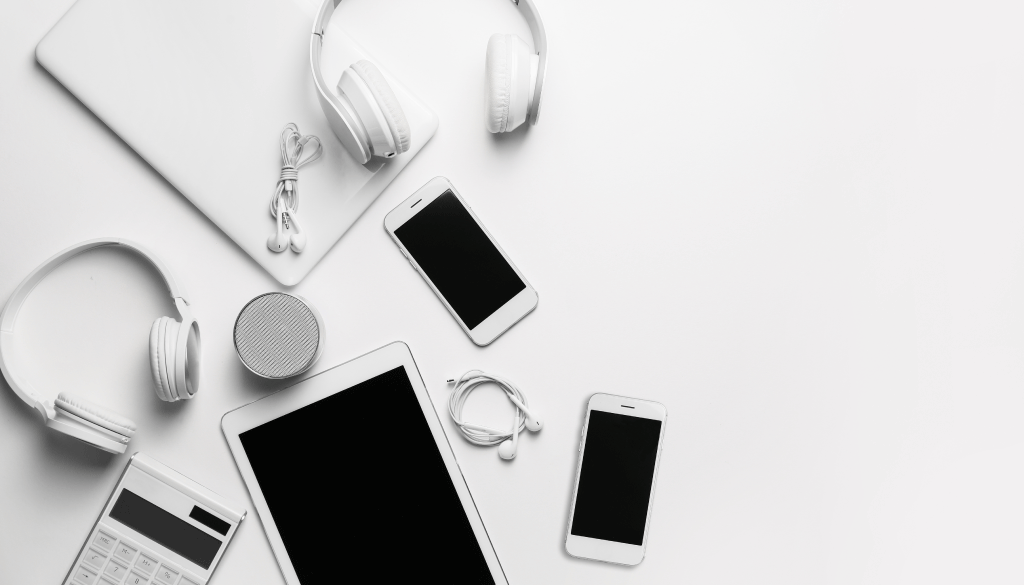
The research was conducted by a team from Virginia Polytechnic Institute and State University, known as Virginia Tech, led by Professor Michael Bartlett, a specialist in mechanical engineering. The team focused on developing circuits capable of facilitating internal connections between electronic components without relying on traditional rigid materials like plastic and metal. Historically, connecting different circuit layers required perforations in circuit boards, which limited flexibility and introduced weaknesses. This new method overcomes these limitations, enabling devices to maintain their integrity and functionality even under constant movement.
The innovative process employs microdroplets of liquid metal that form a kind of three-dimensional staircase between the circuit layers. This method creates what researchers call conductive “vias,” which allow the flow of electric current between layers without the need for holes in the structure. To control the formation of these vias, the researchers apply the liquid metal droplets onto a photosensitive resin. When exposed to ultraviolet light, the resin develops controlled irregularities that guide the droplets into an organized 3D pattern, facilitating electrical conductivity and enhancing the material’s durability.
Beyond its advanced structure, the technology is incredibly versatile and can be applied to various materials, including fabrics. This feature makes the method highly appealing for the creation of “smart textiles” that can be integrated into clothing and wearable accessories, opening up a world of possibilities for functional electronics in everyday life. Imagine, for example, a shirt with embedded sensors to monitor heart rate or detect changes in body temperature, or workout gear that tracks muscle movement in real time. Such devices could benefit not only consumers but also professionals in healthcare, fashion, sports, and safety.
Durability is another essential aspect of this new approach. Thanks to the malleability and resilience of liquid metal, the circuit is less prone to damage than conventional devices, making it better suited for applications requiring both flexibility and robustness. This means that circuits made with this technology can withstand wear and continuous movement, extending their use in long-lasting devices with reduced maintenance needs.
Professor Bartlett highlighted the importance of this new method for soft and wearable electronics: “By integrating circuit layers both in-plane and in-depth, we’ve been able to create complex and flexible multilayer structures with strategically organized parallel vias. This type of organization is crucial for soft electronics, where vias and interconnections are strategically formed to enable the development of electronic devices that respond to user and environmental demands.” He believes this advancement will lead to sophisticated devices that adapt to the human body and its needs, expanding the concept of wearables beyond what we imagine today.
This technology is not only innovative in terms of design and materials but also represents a significant step toward more sustainable and durable electronics. By eliminating the need for rigid and perforated components, there is a substantial reduction in material usage and resource consumption, which is beneficial from an environmental perspective. Moreover, more durable devices mean fewer discarded electronics, contributing to lower environmental impact.
In the near future, these flexible circuits are likely to be applied to a wide range of devices, such as foldable smartphones and tablets, smart wristbands for health monitoring, self-heating clothing for cold days, and even accessories that connect to the internet and adapt to the human body. Each of these products represents a potential application field for soft electronics, and the new liquid metal and 3D vias approach is key to turning these projects into reality.
This technology also has the potential to significantly advance robotics. Robots built with flexible circuits could operate in tight or hard-to-reach spaces, such as rescue areas, research labs, and even hospital settings, where smaller, adaptable devices could perform tasks with greater precision. In medicine, this discovery could drive the development of minimally invasive devices capable of moving with the body and conducting measurements or interventions with minimal discomfort to the patient.
Therefore, this new flexible circuit technology represents a major milestone for the future of electronics, broadening the possibilities for wearable devices, soft robotics, and portable electronics. As these circuits begin to enter the market, they could become commonplace in our daily lives, integrating into what we wear, touch, and use to connect, monitor health, entertain, and even address sustainability challenges.